Pulp Mold Die Supplied by AGICO
AGICO manufactures a series of paper tray making molds of different sizes, such as egg tray making mold, egg carton making mold, seedling tray making mold, shoe insert tray mold, fruit tray making mold, etc.
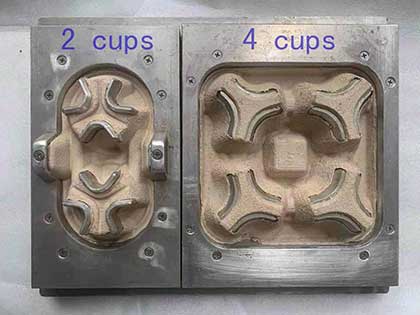
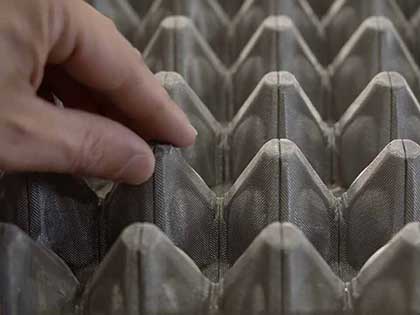
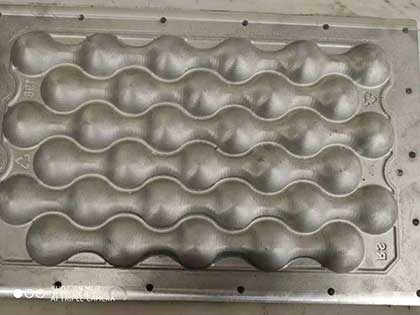
Pulp mold die produced by AGICO works well on both reciprocating machine and rotary drum pulp molding machines, which are used in paper tray production lines of egg tray, egg carton, fruit tray, apple tray, coffee cup tray, shoe insert tray.
How is Pulp Mold Die Produced
Mold Design
Designers analyze and comprehensively calculate the usage requirements of the mold, and draw up preliminary mold design drawings. After the preliminary design is completed, it needs to be reviewed to confirm whether the structure, size and other parameters of the mold are reasonable and feasible, and whether they meet the customers’ requirements. After repeated modifications and reviews, the final draft is confirmed.
Mold Manufacture
Manufacture the upper mold, lower mold, mold supports, and other components separately. This requires the use of various machine tools such as milling machines, drilling machines, grinding machines, etc., to ensure that the dimensions accuracy and surface finish of the mold meet the requirements. The manufactured mold needs to undergo processes such as heat treatment, sandblasting and other processes to increase the strength and durability of the mold.
Precision Machining
This is to ensure that the precision and surface quality of the mold meet the requirements, thereby ensuring the processing accuracy and surface quality of the subsequent aluminum products. Precision machining includes processes such as planetary grinding, grinding, electrical discharge machining, polishing, etc., among which electrical discharge machining is an important step, especially for deep hole and non-circular hole machining, ensuring high precision hole diameter and hole wall quality.
Assembly and Debugging
When the machining accuracy and surface quality of each component of the mold reach the specified standards, the mold needs to be assembled and debugged. After assembly, the mold needs to be debugged, tested, and verified until all working parts cooperate reasonably, achieving the best processing effect and surface quality.
Detail Drawing of Dies
Customer shall provide the dimension details of pulp molding die, it’s simple if you can show us the design of pulp molded tray product, then our engineer can modify according to your need and design the exact pulp molded die to fit your final product.
Material Options
The mostly used material for pulp forming mold die is casting aluminum and plastic; hot press molds are made of aluminum and steel, brass is a extra option for customer if you need it.
CNC Machining Equipment
AGICO adopts CNC for pulp molded tray die production, which is a essential equipment for the accuracy level of pulp tray molded die, it will have a longer service life with good working performance.
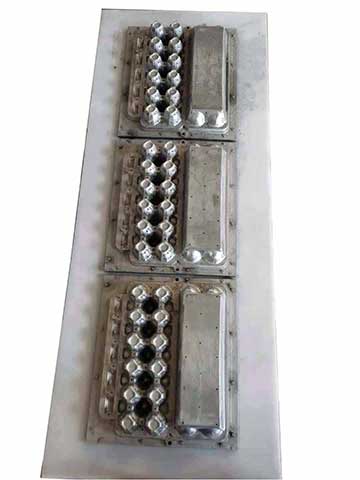
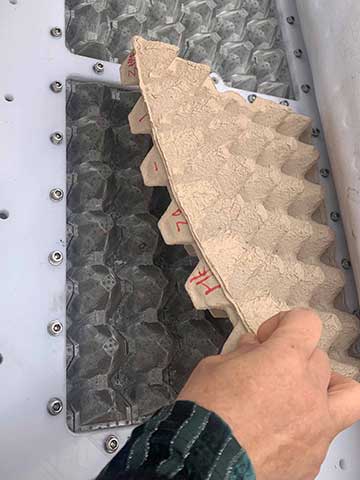
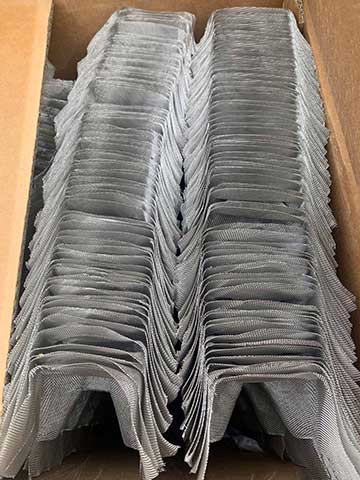
Drill Holes for Pulp Suction
Drill suction holes on the surface of pulp molded dies, this design ensures the sufficient suction force and blow performance in the pulp molded process.
Welding Stainless Mesh
Stainless steel mesh works by separate the air force evenly so that the pulp will form an even and smooth surface in the pulp tray molding.
Assembling on Panel
Install the steel mesh by pressing it tightly on the mould, and fasten the mould unit on the base plate to make one complete set of pulp mold die.
Testing mould
We will make running test of the pulp mold die and provide samples to customer before delivery.