High Energy Consumption Problem In The Drying Process
With the rapid development of the pulp molding industry, automated eggtray production lines have gradually become popular, but the high energy consumption problem in the drying process has always been the core pain point. Paper trays and egg trays are important packaging materials for protecting fragile items such as poultry eggs and electronic products, but with low added value, so manufacturers need to improve their competitiveness by improving quality and reducing costs. However, the traditional drying process has high energy consumption and low efficiency, which seriously restricts production benefits. AGICO will deeply explore the energy consumption problem in the paper tray production process and analyze the innovative direction of energy-saving drying technology.
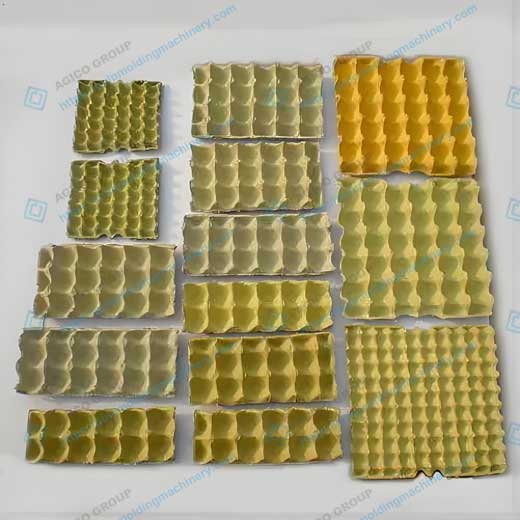
Energy Consumption In Egg Tray Production Process
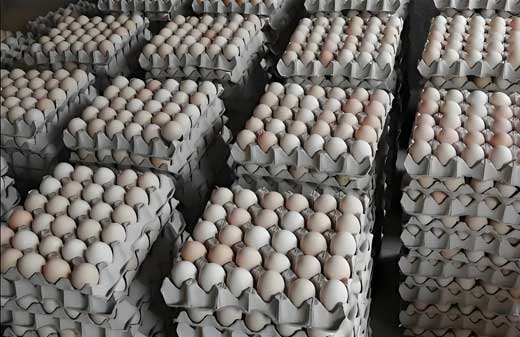
Paper egg tray production mainly includes 4 major steps: waste paper recycling, pulping, forming, and drying. The energy consumption of the drying process accounts for as much as 60%-70%. The following is an optimization analysis of the production process:
Waste paper recycling and pulping
- Raw material processing: Recycled waste paper needs to be thoroughly cleaned of impurities (such as iron wire, hemp rope, and soil) to avoid affecting the quality of the pulp.
- Pulp preparation: Adjust the pulp concentration to 0.5%-1%, and add moisture-proof, anti-corrosion and other additives as needed to ensure product functionality.
Vacuum adsorption molding
- Mould control: The vacuum pump suction force needs to be precisely adjusted (large suction force may damage the mould, small suction force may cause the product to become loose).
- Mold maintenance: Clean the mold surface regularly to ensure molding accuracy and consistency.
Drying process
- Initial moisture content: The moisture content of the paper tray after forming is about 150-180 grams, and it is necessary to reduce the humidity to below 60% through efficient dehydration.
- Traditional problems: Hot air drying relies on coal or gas, which has high energy consumption and unstable temperature and humidity control, which can easily lead to product deformation or uneven drying.
The Root Causes Of High Drying Energy Consumption
- Technical limitations: Traditional drying equipment relies on a single heat source, has low thermal energy utilization, and lacks an intelligent temperature control system.
- Process defects: static drying mode is inefficient and batch processing time is long (usually 8-12 hours).
- Seasonal influence: Paper tray production needs to run continuously throughout the year, and the energy consumption of traditional equipment increases sharply in low-temperature and high-humidity environments.
Energy-Saving Solution: Technological Breakthrough Of Cabinet Tray Dryer
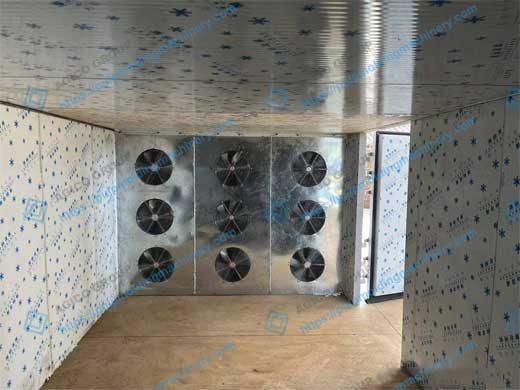
In response to the above pain points, Cabinet Tray Dryers have become the preferred solution for industry upgrades. Its core advantages are as follows:
Technical characteristics | Traditional drying equipment | Air energy heat pump dryer |
Energy efficiency | High (fossil fuel dependence) | Energy saving over 70% (1 kWh of electricity ≈ 4 kWh of heat) |
Temperature and humidity control | Manual adjustment, large fluctuations | Fully automatic intelligent temperature control, error ≤±1 ℃ |
Drying time | 8-12 hours/batch | 3-4 hours/batch |
Environmental protection | High carbon emissions | Zero emission, in line with green production standards |
Applicable scenarios | Single fixed material | Supports paper trays, egg trays, corrugated paper and other materials |
Core Function Of Cabinet Tray Dryer:
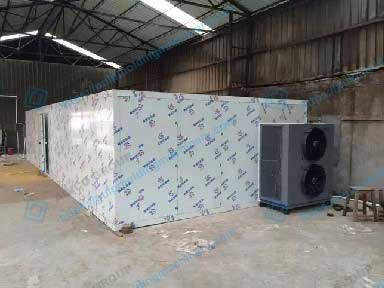
- Heat recovery system: Recover waste heat through condensation and dehumidification to improve energy utilization.
- Multi-mode drying: supports side blowing, top blowing, and tunnel circulation, adapting to different paper support structures.
- All-weather operation: Stable operation in -10 ℃ to 45 ℃ environment, breaking through seasonal restrictions.
Experts Suggest: Optimize The Entire Production Process
Equipment selection:
Give priority to fully automatic air-energy heat pump drying units, equipped with Internet of Things modules for remote monitoring.
Process collaboration:
- During the molding process, the vacuum adsorption parameters are optimized to reduce the initial moisture content.
- Use mold preheating technology to shorten the drying time.
Intelligent Operation and Maintenance:
- Clean the drying room filter regularly to ensure the efficiency of hot air circulation.
- Use big data to analyze energy consumption peaks and optimize production schedules.
Case reference: After a medium-sized paper tray factory introduced an Cabinet Tray Dryer, the energy consumption cost of a single batch dropped from 18 yuan (approximately $2.47) to 5 yuan (approximately $0.69), saving more than 500,000 yuan (approximately $68,650) in electricity bills annually, and the investment payback period was only 1.5 years.