Pulp molding, as a representative of green packaging that is currently in the limelight, is favored by brand owners. In the production process of pulp molded products, the mold plays a crucial role. Its development and design require high technical requirements, significant investment, long cycles, and also involve certain risks. So, what are the key points and considerations in the design of pulp molding molds?
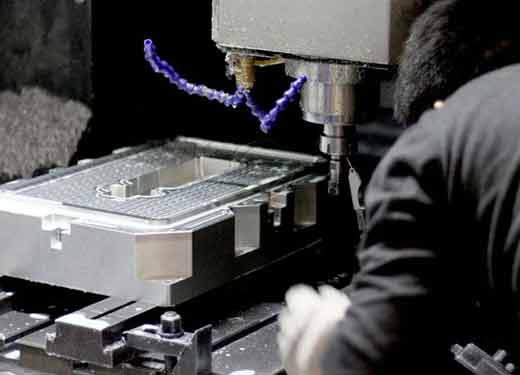
Characteristics of Pulp Molding Molds
Mold design must meet the structural requirements of pulp molded products and also comply with the requirements for mold design and manufacturing while meeting the usage and forming process conditions.
Therefore, before designing pulp molding molds, it is necessary to thoroughly analyze and study the structure of pulp molded products in order to ensure the economic rationality, technical feasibility, coordination, and unity of both product design and mold design.
During the forming process of pulp molded products, they need to go through the mold multiple times to complete the manufacturing process. This is because pulp molded products are formed on a single convex or concave mold and must be transferred to the wet pulp in the mold cavity after the convex and concave molds are closed. The transfer to the forming mold is accomplished by applying pressure and heat.
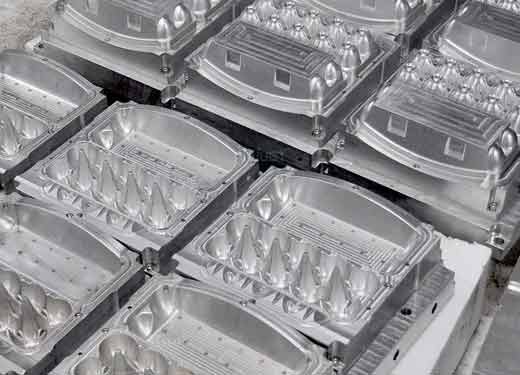
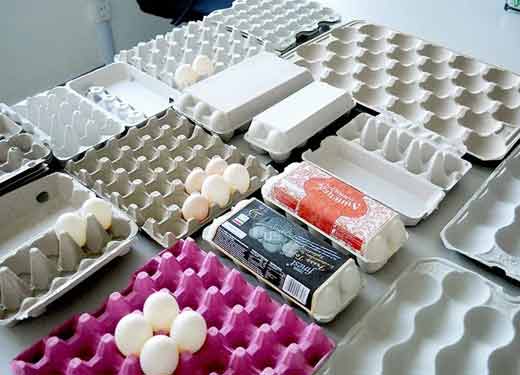
As a result, pulp molding molds are divided into forming molds, shaping molds, finishing molds, and cutting molds. There are two types of forming processes: absorption forming and pressing forming. Pressing forming molds are somewhat similar to rubber and plastic molds, while absorption forming molds are more unique and complex.
AGICO Pulp Molding Molds
The field of pulp molding has seen a wide range of applications, particularly with the growing global emphasis on eco-friendly packaging and products. The types of molds and their applications are as follows:
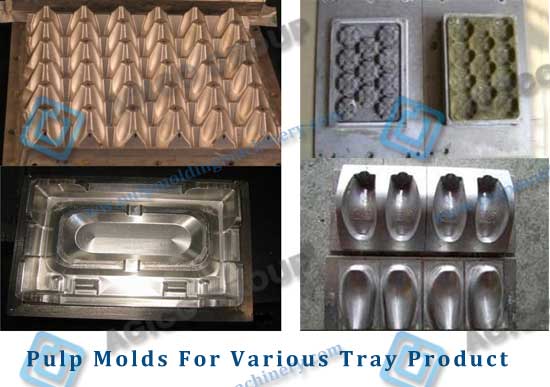
- Packaging Molds: These include molds for egg trays, fruit trays, bottle trays, industrial product packaging, and electronic product packaging, among others.
- Mold Application: These encompass a variety of products such as shoe insoles, paper plates, paper lunch boxes, coffee cup carriers, seedling trays, specialty paper tubes, paper urinals, toilet seat covers, paper masks (props), and loudspeakers, to name a few.
Manufacturing of Pulp Molding Molds
- Materials used for mold manufacturing typically fall into two categories: plastic molds and metal molds.
- The manufacturing process for molds varies greatly based on factors such as shape requirements, precision requirements, environmental conditions, and the quantity of molds needed. Common manufacturing techniques include CNC machining, precision casting, compression molding, precision welding, injection molding, drilling and cutting, and precision hand polishing, among others.
Pulp Molding Molds Classifcation
Absorption Forming Mold:
An absorption forming mold consists of a convex mold, concave mold, mesh mold, mold base, mold back cavity, and air chamber. The mesh mold, which is woven from 0.15mm diameter wires (metal or plastic), cannot independently form and must be attached to the mold surface to function.
The mold back cavity is a cavity located on the mold’s backside, which maintains a certain thickness and shape that synchronizes with the working surface of the mold base. The convex and concave molds form a shell with a certain wall thickness. The working surface and the back cavity are connected by evenly distributed small holes.
The mold is installed on the forming machine’s template through the mold base. The other side of the template has an air chamber, which is connected to the back cavity. It also has 2 channels for supplying compressed air and vacuum pressure.
The allowance for absorption forming molds: The allowance for absorption forming molds is a critical aspect of mold design.
Pulp Molding Shaping Mold
The shaping mold is a mold with heating, pressure, and dehydration functions that the wet pulp directly enters after forming.
The shaping mold is used to dry and shape the wet blanks in the mold. The products made with shaping molds have smooth surfaces, accurate dimensions, solidity, and good rigidity. Disposable tableware is manufactured using this type of mold. In industrial packaging, small, precise, and large quantities of small items are packaged by stacking layers, and packaging products are used to position and package between each layer. If pulp molded products are used, shaping molds are needed for manufacturing.
However, general industrial inner packaging products work on a single surface and do not require thermal shaping. They can be directly dried. The structure of shaping molds includes a convex mold, concave mold, mesh mold, and heating elements. The convex or concave molds with the mesh mold have drainage and vent holes. During operation, the wet blanks in the shaping mold are first subjected to squeezing, squeezing out 20% of the water. At this point, the wet blanks contain 50-55% water. After heating in the mold, the remaining water is evaporated and expelled. The wet blanks are squeezed, dried, and shaped to form the products.
The mesh mold in the shaping mold can cause web marks on the product surface and is prone to damage during frequent squeezing. To address this issue, some mold designers have developed a meshless mold made from copper-based spherical powder metallurgy. After multiple structural improvements and selecting appropriate powder particle sizes over two years, the meshless shaping mold has a lifespan ten times longer than that of a mesh mold, a 50% reduction in cost, and produces highly accurate paper products with smooth internal and external surfaces.
Pulp Molding Finishing Mold
After drying, the wet pulp undergoes deformation, and in some cases, certain areas require high precision in the final shape of the product. In such cases, a finishing process is necessary, which involves the use of a finishing mold. This type of mold also requires heating elements but does not need a mesh mold. The products that require finishing need to retain 25-30% moisture content during drying to facilitate the shaping process.
In production practice, it is challenging to control the moisture content, making it difficult to meet quality requirements. Some manufacturers have designed a spray finishing mold, which has spray holes corresponding to the areas that require finishing. During operation, the completely dried product is placed in the finishing mold, and when the mold closes, the spray holes on the mold apply a spray of heat and pressure to the product. This type of mold is somewhat similar to a spray iron used in the garment industry.
Cutting Mold
A cutting mold is used to trim the product edges and is also known as a trimming mold.
New Trend in Pulp Molding Mold Design: Universal Mold
Pulp molding utilizes molds to shape paper products from pulp. Therefore, molds play a crucial role in pulp molding technology. When producing disposable tableware, gift box packaging, cosmetic packaging, and other products with relatively simple shapes that require some degree of universality, a universal mold can be used.
In situations where there are budget constraints or tight timelines, a universal mold can be used for various product packaging requirements. Pulp molding packaging suppliers can continuously innovate based on a basic universal mold, adjusting the form of the inner lining and the external packaging to match the packaging needs of different products. By customizing the surface pattern (such as embossing, high gloss, or hot stamping), pulp molding packaging can become highly versatile and distinctive.